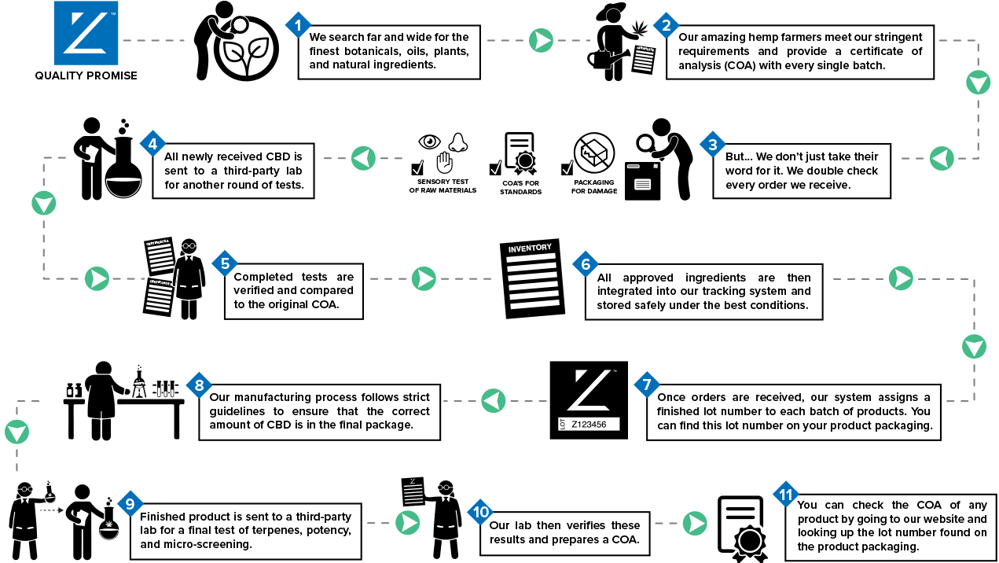
From Farm To Lab
Here at Zuna Brands, we believe in the following:
- Holistic approach
- Complete transparency
- Intential manufacturing
We are there every step of the way ... beginning with each harvest at our local Hemp farms to our certified manufacturing facilties onto you, the customer.
Here is an overview of our manufacturing and quality control processing as depicted in the image above:
Source Raw Materials (CBD, Oils, Butters, Salts, Etc.)
- Before purchase we do vendor approval, check for their internal quality controls and product quality. - After approval we can place orders.
- Purchase Raw Materials (CBD, Oils, Butters, Salts, Etc.)
Quality Control
- QC 1: Create Purchase order (Their internal QC team provides a COA (Certificate of Analysis) for products purchased. o For CBD this includes Pesticides, Heavy Metals, Potency, Residual Solvents testing.
- QC 2: Receive incoming material (All Materials on HOLD until they pass our QC Procedures)
- CBD tested again for Pesticides, Heavy Metals, Potency, and Residual Solvents.
- Oils, Salts, Butters, Etc. are checked for organoleptic properties and their incoming CoA is compared to previous Standardized CoA to ensure quality is within Spec.
- Approval: If material are approved they are officially released into inventory and assigned their own lot numbers and can be used for production. (See next point)
- Denial: If material is denied, the products are placed into quarantine and are either returned to vendor for remediation if possible or are removed from system and not used for production.
Production of Products
- Incoming Orders: These are placed into the system and the raw materials are booked and Lot Numbers are assigned for the full batch’s Manufacturing Order.
- Production: Raw Materials are logged with their individual lot numbers for traceability and finished goods are packaged and labeled with the finished Lot Number assigned from the Manufacturing Order.
- Finished Goods QC 3: Products are placed on internal QC hold while a 3rd Party tests finished products for Potency, Micro Screening, Terpene Profile and Residual Solvents (Solvents: this changes on products depending on their ingredients). These tests have a general turn around time of 3-6 days and WILL NOT LEAVE THE WAREHOUSE WITHOUT PASSING.
- Pass:
- This internal CoA will be combined with the 3rd party test results and will be available online.
- The Finished Lot numbers that were assigned via the Manufacturing Order will be used on products on CoAs as the search variable online. (See CoA How – To document for reference.)
- These products are now available for sale and COAs will be sent with each shipment of product to the fulfillment warehouse. (See next point)
- Fail:
- Remediation: If products can be remediated and pass upon secondary testing with 3rd party lab, they can be sold.
- Destruction: If products fail micro screening or solvents, the products are sent for destruction according to product type and GMP guidelines.
Shipping Customer Orders